 |
|
 |
 |
 |
 |
 |
 |
Paddle/Ribbon Mixers
|
 |
Quality Mixers
Most of the products in use today are combinations of more than one ingredient and mixing is one of the most common of all processes.
IMPEC manufactures equipment for mixing solids to solids and liquids to solids.
This basically includes free flowing materials such as dry powders, granules, slurries and some pastes.
IMPEC mixers incorporate stationary vessels with rotating internal agitators, designed and built to accommodate production requirements.
Processing plants, research and development laboratories, universities, pilot plants, institutions and testing facilities throughout the world are only some of the businesses using mixers as part of their operations.
Foods, chemical compounds, plastics, agricultural materials, aggregates, pharmaceuticals, bakery premixes, and animal feeds are examples of the products that have been successfully mixed.
IMPEC, offers two basic types of horizontal mixers, "Batch" and "Continuous" with two different types of agitators: "paddle" and "ribbon" (described below).
|
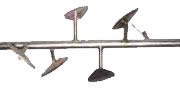
Click the image for a product demonstration.
|
Batch Mixers
Batch Mixers are individual, free standing machines in which the ingredients are loaded, agitated and then discharged, typically into holding bins, smaller containers or packaging equipment.
Batch mixers may be fitted with either paddle or ribbon agitators and may have either center or end discharge locations.
|
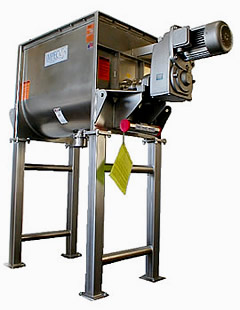 |
Continuous Mixers
Continuous Mixers are integral parts of large production lines and continuously discharge finished product into the next piece of equipment in the process.
A continuous mixer is constantly fed with the correct amounts and proportions of ingredients at one end. As the materials are being mixed, they are also conveyed to the opposite end where the product is discharged.
Continuous mixers generally have paddle type agitators with a series of mixing "stages" that progressively move and blend ingredients.
|
Paddle Agitators
Paddle Agitators lift, tumble, divide and circulate materials in an intense yet gentle mixing action, which provides relatively fast mix times.
This permits more batches to be mixed per shift, reduces product damage due to heat or degradation and minimizes wear and tear on the machine. Close paddle blade to trough clearance provides nearly complete discharge of product.
Full batches with additives as low as 1% may be uniformly mixed. Quantities as small as 20% of capacity may be blended with the same accuracy as a full batch. Mixing of dry, free-flowing materials typically takes 3 to 5 minutes.
Of course actual mixing times will depend on the ingredient characteristics, proportions and amounts.
|
Ribbon Agitators
Ribbon Agitators use opposing inner and outer helical flighting, which produces an end-to-end, side-to-side mixing action, sliding ingredients along the main shaft, separating and redistributing the materials behind the flighting.
Product levels in these machines must be high enough to reach the lower arc of the inner ribbon flighting in order to mix thoroughly. Ribbon mixers may be configured for either end or center discharge locations.
Agitators are furnished with single or double inner and outer flighting as required.
|
|